The quest to cut the cost of electric-vehicle motors by adopting new material solutions
As sales of electric vehicles (EVs) rise, makers of electric motors ("e-motors") for EVs are under pressure to develop smaller, more efficient high power density motors in a cost-effective way. In this quest most motor manufacturers have opted to use the Permanent Magnet Synchronous Machine (PMSM) since this type of motor has a higher efficiency and occupies less volume compared to other types of e-motors - put simply, it's smaller & more energy efficient. Further, if power density is defined as power per unit volume, then the PMSM offers relatively high power density when compared with alternatives.
Nevertheless, the PMSM does have certain limitations. Electrical power can be constrained by mechanical losses in the bearings, windage and core, where eddy currents, hysteresis and Joule heating may occur. The PMSM is also designed to cut off at temperatures that threaten to damage its internal insulation, so thermal management is a crucial performance factor for e-motors for electric vehicles – the design of the insulating system is, clearly, instrumental.
The PMSM also poses cost restrictions, particularly since it uses rare-earth (RE) magnets, which typically represent 50-55% of the raw material costs. Reducing the amount of REs used will significantly reduce the cost of a PMSM – and contribute to save valuable resources.
One way to do this is to improve the PMSM's internal insulation through the use of impregnation resins and phase insulation papers. For distributed winding machines the slot liner and the impregnation resin offer considerable opportunity to improve thermal management, and their use will, in turn, enhance the motor's efficiency. Typically, the insulating materials used in the slot liner are meta-aramid paper in a laminate form, with a polymer film in the center. A range of polymer films can be used, depending on performance and cost requirements.
What does the ideal the ideal slot liner material look like?
The ideal slot liner material is reliable under peak loads and has improved mechanical properties, reducing the risk of winding defects while increasing puncture resistance, which then allows an increase in copper density and the slot-fill ratio. The design engineer's dream is for a thinner slot liner at the same breakdown voltage, with winding temperatures reduced through the use of an insulating material with a higher thermal conductivity than that of meta-aramid paper. The insulator should also be reliable in harsh environments, and able to resist hydrolysis and aggressive chemicals.
In search of the "dream" slot liner insulator, Victrex engineers undertook a simulation of replacing a 250-micron meta-aramid-PET-laminate slot liner material with 150-micron APTIV™ film. Working in collaboration with Motor Design Ltd., which specialises in simulation software that can help to enhance the performance of electric motors and optimise their cooling, they simulated a test on a 2012 model Nissan Leaf, using an 80kW PMSM.
Promising simulation with APTIV™ film solution
- Using a 40% thinner and more thermally conductive thermoplastic slot liner film enables improved heat flow from the wire windings to the stator iron and outer-water-jacket cooling system.
- The excellent thermal conductivity of APTIV™ film enables improved thermal management and reduction of peak winding temperatures by 2-3°C, compared to traditional laminates, and helps the e-motor stay cool.
- With improved thermal management and thinner slot liners there is a potential increase in copper density (i.e., the slot-fill factor) of 2%.
- There was a 5% increase in torque output – this translates into higher power output for a same-size machine.
Aim: cost savings through adoption of new slot liner solution
Admittedly, APTIV™ film is a more expensive insulator than a typical meta-aramid paper. But there is a cost reduction potential when the same performance is obtained from a smaller machine since axial length can be reduced without compromising continuous torque output or reliability. This enables a reduction in the e-motor bill-of-material costs as the volume of iron and RE magnets can be reduced, decreasing the weight of the machine and ultimately the vehicle itself, potentially reducing fuel costs.
What is more, with a costing model based on a joint study by Newcastle University and Jaguar Land Rover (JLR), the Motor design Ltd. simulation concluded that there could be a US$6.0 cost reduction per motor.* In other words: using a higher- value thermoplastic insulating material, in this case APTIV™ film from Victrex, may allow enhanced machine performance, enabling a total material cost saving per motor – and end the quest for the ideal slot liner material.
More details on Benefits of APTIV™ film insulation systems in e-Motors , a webinar on-demand.
*Rare-earth magnet prices are heavily dependent on the dysprosium and terbium content, both used in small amounts to raise temperature resistance and to give the magnets their desired shape – curved magnets are much more expensive due to manufacturing costs. The 2017 pricing used in this “US$6.0” model assumes basic straight-shaped NeFeB magnets, such as the N35EH grade.
Electrical-steel pricing is at the lower end of the unit-cost range (US$2.35-2.50) and assumes a “stamping” process rather than higher- cost laser-cut processing.
The copper costs remain the same because copper usage is reduced with the shorter axial length, but the copper density (slot-fill factor) is increased when there is a thinner slot liner.
© Victrex plc. 2018. All rights reserved.
Disclaimer
About the author
James Bonnett is Global Program Manager for E-mobility in the Automotive business unit at Victrex and the company’s subject matter expert for Electrified powertrains in particular e-motors. He has been with the company since 2014 and has previously held business and product development roles at Umeco and Project engineering positions at Cobham Group. With over 15 years’ experience in both composites and polymer industries, James has a Mechanical engineering degree from Leeds University (BEng) in 2001 and later went back to Leeds to complete his MBA in Manufacturing Leadership in 2011
About the author
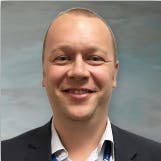