Key elements of a successful thermoplastic gear solution for power transmission (Part 1)
Like many products, a successful thermoplastic gear solution for metal replacement within a power transmission application must be commercially compelling, technically feasible, and provide a desirable performance benefit. But, what do these phrases actually mean within the context of a thermoplastic gear solution, such as in an automotive auxiliary power transmission gear scenario, for example?
A couple of helpful explanations upfront:
- Power transmission application: Fundamentally, a gear train is a mechanical system designed to transmit motion and force. Every gear train will have aspects of both, but for the purposes of this discussion we will differentiate between those whose primary function is actuation (a throttle body actuator for example) versus those whose primary function is transmission of mechanical power (such as the transmission in your vehicle) – with the latter, the focus of this article.
- Gear solution: At first, it might seem odd to characterize a single gear component as a “solution” considering its reliance on the overall system to fulfil a function. However, it is this interdependence of system and gear that distinguishes a gear component from a gear solution. The success of a gear solution is not measured by a single component but by the overall performance of the system which contains that component. The sound level of a gear solution is not judged by the noise of the gear component alone but by the noise level of the system that contains the gear, just as a lower part cost that increases the complexity, and therefore cost, of the overall system would not be considered commercially attractive. We can consider the gear solution to be the reliable delivery of a quantitative system benefit including the manufacturing, delivery, supply, assembly logistics and efficiency of that benefit.
So, what makes a successful thermoplastic gear solution in a power transmission application? Well, that requires holistic consideration and delivery of the following elements.
Desirable performance
Firstly, a successful thermoplastic gear solution must enhance the overall system performance in some quantifiable manner. For a thermoplastic gear replacing a metal gear, or gear system, this is commonly one of the following elements.
- Noise, vibration, and harshness (NVH) improvement. NVH represents how a system or vehicle sounds and feels to the end user. It is often seen as a measure of vehicle quality especially in an age of increasing electrification where vibration and noise is no longer masked by the sporty growl of the internal combustion engine (ICE). Due to the significantly softer mechanical properties of thermoplastics as compared to metals, as well as the increase in design flexibility that accompanies the injection molding (IM) manufacturing process, a well-developed thermoplastic gear solution is often able to mitigate gear rattle generation and attenuate NVH transmission to an extent unachievable by all but the most complex metal gear systems. However, as it is the NVH of the system that determines success or failure of a thermoplastic gear solution, each gear must be tailored to the system’s NVH characteristics to ensure coupled NVH effects such as resonance are avoided.
- Weight & inertia reduction. The weight of individual components and the inertia of rotational components directly and indirectly impact vehicle efficiency. Most directly, the component weight contributes to the overall vehicle weight and a weight reduction in a particular part can either be reassigned to a more valuable component (such as a battery in an electric vehicle (EV)) or eliminated entirely for increased vehicle performance. Rotational inertia, assuming the system is not regenerative, results in energy loss and an increase in response time during any system acceleration. For a thermoplastic gear solution, weight reductions of 40% and inertial reductions of 60% are often achievable as compared to an equivalent metal gear solution.
Admittedly, commercial viability, and technical feasibility are equally important elements. Exactly for that reason, part 2 of this blog will examine these aspects of an innovative turn-key solution for high-precision thermoplastic gears.
About the author
Joseph Elmquist joined Kleiss Gears in 2013 as a lead design engineer and technical lead for new product development of thermoplastic and thermoplastic composite gears. Following Victrex’ acquisition of Kleiss in 2015, he continued to lead the technical development efforts on thermoplastic powertrain gear applications culminating in the successful launch of the first VICTREX PEEK gears for power transmission within the automotive powertrain in 2017. Joseph holds a BS in Engineering Mechanics and a MS in Mechanical Engineering with a focus on nonlinear dynamic mechanical systems from the University of Wisconsin-Madison.
About the author
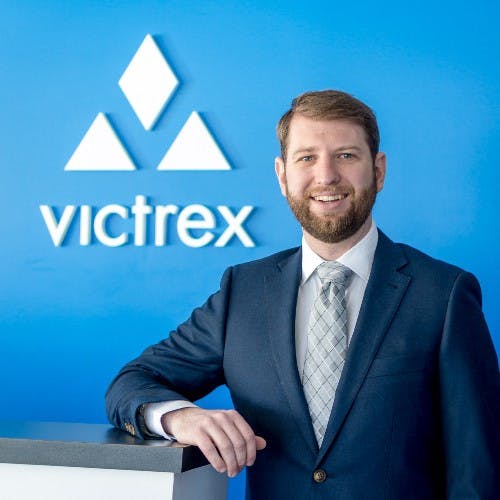