自动化在复合材料生产中的重要作用
在航空航天领域,自动化是提高热塑性复合材料部件制造水平的重要手段。飞机制造商(OEM)和各级零部件供应商采用LMPAEK等高性能聚合物并结合新型加工技术,有望通过轻型复合材料来增加产能、减少缺陷、提高效率,进而降低生产成本。
复合材料技术所带来的轻量化和机械性能优势已得到广泛认可。自用于飞机制造以来,复合材料在该行业一直保持稳定增长,预计到2026年将达到4.65亿美元。展望未来,复合材料尤其是热塑性复合材料单向带在降低系统成本和提高产能方面可为航空航天业带来更大优势。可以说,热塑性复合材料是一种适用性更强的生产材料。它可以重复加工,无放热风险,不太可能受到异物碎屑的影响,同时还可以提高加工速度,使生产线更加清洁,并加快实现大批量生产。
尺寸均匀一致:单向带
热塑性复合材料单向带(TPUD)常被用于自动化生产,因为其尺寸均匀(宽度、厚度一致),孔隙率低,在大规模生产时具有一定的可预测性。如今,我们研发出了各种专用非高压釜制造工艺,以充分利用热塑性复合材料的潜能。
以下皆为高度自动化并且已经实现商业化的制造技术:
- 自动铺带(ATL)和热压固化
- 现场自动铺丝(AFP)
- 自动铺丝和真空袋成型
- 自动铺丝和固化炉固化
- 连续模压成型(CCM)
- 纤维贴片铺放(FPP)
- 模压成型
- 编织
然而,自动化生产工艺并非一帆风顺。自从航空航天工业开始使用复合材料以来,手工作业一直是主要的生产方式。从手工作业转变为自动化工艺可以说是自然而然的事,但是工艺和检测技术的验证并使其成为规范需要一定的时间。如今,为正确的应用选择合适的材料成为了一大挑战。
采用热塑性复合材料与采用金属材料的设计为何大相径庭呢?
对于设计工程师而言,金属材料和复合材料属于不同的知识领域,后者具有各向异性(即方向性)。如果您需要的是各向同性特性(即在各个方向测量时性能都相同),那么您可能会问为什么要使用各向异性材料呢。原因有二:
- 首先,碳复合材料(密度约为1.6 g/cm³)与常用的航空航天金属材料如铝材(密度约为2.8 g/cm³)和钛材(密度为4.4 g/cm³)相比,密度上存在较大差异:大约比铝材轻三分之一,比钛材轻三分之二。但这不是唯一的原因。
- 其次,我们还需要看材料的比强度(通常称为强度重量比)。铝合金6061-T6和5级钛合金6AI-4V的比强度分别为107和214,而复合材料的比强度达到了1515,真是令人叹为观止。凭借这一特性,即使在施加均匀载荷的情况下,复合材料的表现也可以同样令人信服。它们之间还有一个重要的区别:复合材料的强度具有明显的方向性。
在所受载荷不均匀的应用中,复合材料因为具有各向异性特性,所以可以根据需求进行定制。有了这些定制特性,就可以进一步降低层压板的厚度,从而使其重量比同等性能的准各向同性材料和金属材料更轻。因此,对于与ATL或AFP生产设备打交道的工程师来说,这种设计自由度具有不可思议的价值。
优化性能和制造工艺
在部件设计之初,就需要将制造工艺考虑在内。制造设计可推动应用设计。加工知识对于按时、按预算完成项目目标至关重要。例如,在嵌件注塑工艺中,部件设计能够促进模具设计,还可以通过迭代设计工艺来优化部件的性能和生产可行性。设计复合材料部件与设计金属部件之间的根本区别在于,复合材料部件所用材料价格昂贵,但时间成本不高(因为生产周期短),而金属设计则恰恰相反——材料相对便宜,但时间成本昂贵。 因此,您必须明智地选择合作伙伴,确保他们对现有热塑性复合材料制造技术有深刻的了解。这有助于设计工程师为应用选择合适的工艺和材料组合。
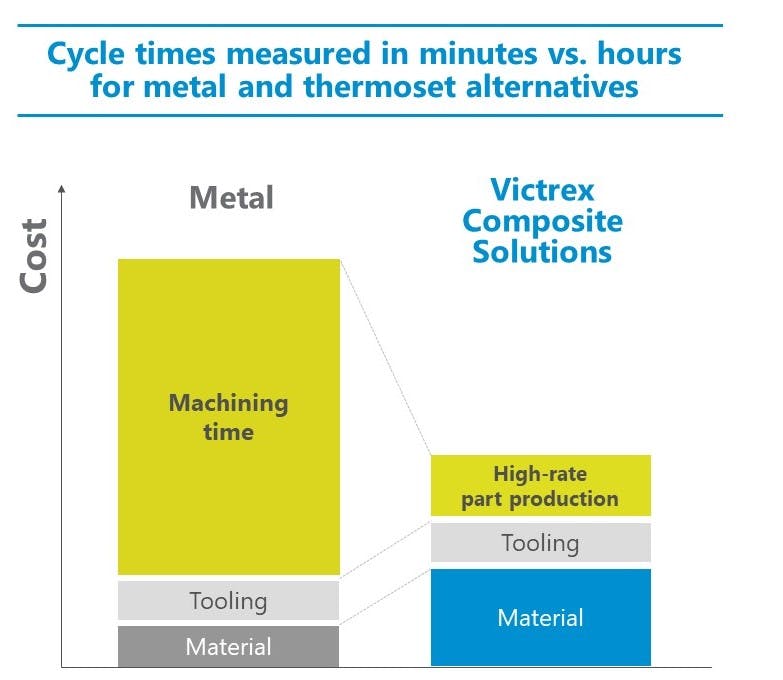
合格材料供应
采用热塑性复合材料的另一大阻力是缺乏有关合格材料的数据库。毕竟,金属材料在航空领域已经使用了超过100年,并且都已经标准化,大部分甚至已经商品化了。而热塑性塑料则更加复杂,因为您需要的不是为特定材料创建数据库,而是需要有关特定热塑性复合材料和制造工艺的数据。随着材料和工艺标准的确立,这一问题会变得越来越无关紧要,但这也表明设计和制造的合作方式对有效实施热塑性复合材料解决方案至关重要。于是,问题就变成了这样:我们应投资于可能处于生命周期末期的成熟材料和技术,还是应跨越鸿沟,开发出新的材料和工艺组合,从而保证未来的效率?如果OEM厂商的投资是一个风向标,我觉得会是后者。
热塑性复合材料前景光明
复合材料在航空航天领域的前景似乎比以往任何时候都更光明。随着热塑性复合材料自动化生产技术的日益成熟和普及,我们发现,商用飞机、先进无人机和旋翼飞机等各种飞机平台对复合材料的使用与日俱增。随着材料鉴定方法的不断进步,以及航空航天业在设计中能够更加有效地利用各种材料和工艺,复合材料解决方案在航空航天领域可能会继续呈现出增长态势,进而研制出可大规模生产的轻型飞机。
关于作者
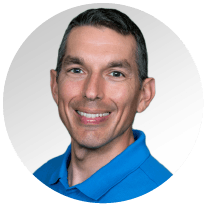