LMPAEK™ Polymers: Transforming the Aerospace Industry

The aerospace industry has always been at the forefront of technological advancements, constantly pushing the boundaries in design, materials, and manufacturing processes. Materials that have recently gained significant attention in the aerospace market include LMPAEK™ polymers. These high-performance polymers are helping revolutionise the industry to achieve lightweight, strong parts with faster processability versus thermosets.
Invention and Early Development:
LMPAEK™ Polymer was invented by Victrex more than ten years ago. It is a Polyaryletherketone high performance polymer for engineering thermoplastics that offers many of the performance attributes of PEEK, but with lower melting properties, melting at 305°C, which is 40°C lower than PEEK. Victrex recognised the potential for this polymer and how it offers an exceptional combination of properties such as high strength, excellent mechanical performance, exceptional resistance to chemicals, and superior flame-retardancy.
One of the primary reasons LMPAEK™ polymers have gained traction in the aerospace market is their lightweight nature and ease of processing, ultimately leading to reduction in production costs. Weight reduction is a critical factor in the aerospace industry, as it directly impacts fuel efficiency and, consequently, operating costs. LMPAEK™ polymers have a significantly higher strength-to-weight ratio compared to traditional metal materials. This allows for the creation of lightweight components without compromising structural integrity and safety.
Moreover, LMPAEK™ polymers offer excellent heat and chemical resistance. This makes them ideal for aerospace applications, where components are subjected to high temperatures, high-pressure environments, and exposure to various chemicals. Traditional materials like aluminum and steel often struggle to withstand such combined conditions, making LMPAEK™ polymer a reliable choice.
Market Adoption and Future Impact:
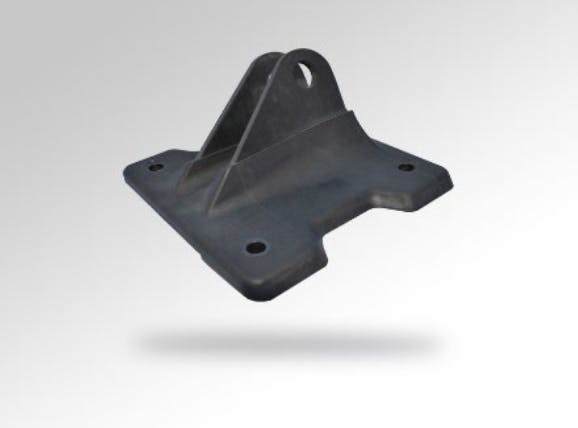
The versatility of LMPAEK™ polymers also opens new avenues for design and manufacturing, especially Unidirectional tape (UDT) with continuous carbon fiber. These polymers when offered as UDT can be easily processed into complex shapes and intricate geometries, allowing for innovative designs that are difficult with traditional materials and manufacturing methods.
Additionally, LMPAEK™ polymers can be processed using techniques such as additive manufacturing, making them compatible with existing manufacturing processes.
Several leading aerospace companies have started incorporating LMPAEK™ polymer UDT, film, filament and compounds in their aircraft and spacecraft designs. These polymers are being used in applications such as structural components, interior panels, and even critical engine parts. The adoption of LMPAEK™ polymer has not only helped reduce weight and improve fuel efficiency but has also enhanced the ability to process tape faster, achieve quality parts, and reduce costs.
A Timeline and Acceleration of Adoption
The year 2020 witnessed a significant increase in presentations and published papers on LMPAEK™ materials, highlighting their growing importance in the industry. During this time, Victrex collaborated with customers, setting new records, and further demonstrating product potential: Composite PAEK Tape | Thermoplastic Tape - Victrex
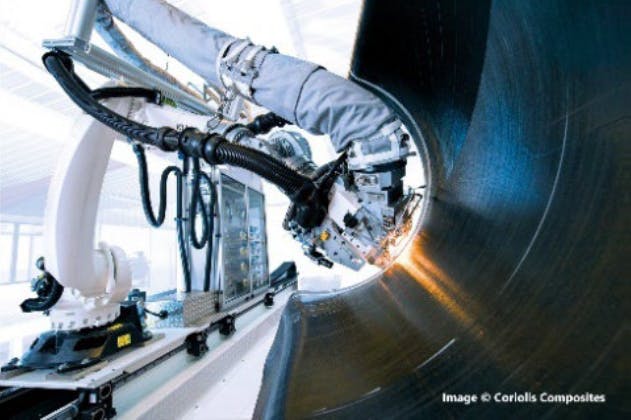
- 2019 Cleansky Program Collaboration with Toray and JEC 2019 A significant milestone was reached when a collaboration was established with Toray on the Cleansky program for the "Aircraft of Tomorrow" with Airbus. The aim was to leverage the unique properties of LMPAEK™ materials to drive innovation and advancement in the aerospace sector.
A turning point for LMPAEK™ materials came at JEC 2019, where a demonstration and presentation showcased the Quantified Value Proposition (QVP) of LMPAEK™ Unidirectional Tape processed by Automated Fiber Placement (AFP). The collaboration with Coriolis demonstrated the high speed, high quality, and exceptional mechanical strength attained through this process. Victrex and Coriolis Composites to unlock efficiency potential for thermoplastic composite parts.
- 2020 Electroimpact achieved thermoset-like production speeds of 4,000 inches per minute, emphasizing the efficiency and productivity of LMPAEK™ materials. At CAMX 2021 this received the Material Process Innovation Award. Victrex UD Tape Helps Electroimpact Improve Thermoset Layup Speeds (plasticstoday.com)
- 2020 French aircraft manufacturer and equipment supplier Daher to produce an exceptionally 176-ply laminate structural aircraft panel, with a thickness of 32 mm, opening the opportunities for thick structural parts like wing ribs. Victrex and Daher: Breakthrough for next-generation thermoplastic composite materials for structural aircraft parts
- 2021 The Multifunctional Fuselage Demonstrator (MFFD) project made its first public announcement. The upper half of the MFFD was developed by DLR (Germany) and the lower half by NLR (Netherlands). This project showcased the versatility and potential of LMPAEK™ materials for multifunctional aerospace components. Manufacturing the MFFD thermoplastic composite fuselage | CompositesWorld
- 2022, at various conferences and exhibitions key customers showcased their demonstrators and showed the possibilities of how LMPAEK™ materials can make an impact on manufacturing.
- 2023, larger dimension parts and structures were demonstrated at JEC 2023 with companies exhibiting parts made entirely of LMPAEK™ based materials for the first-time earning recognition within the composite industry. JEC Composites Innovation Award 2023 winners | CompositesWorld
- 2025, The innovative use of LMPAEK™ materials in the Multifunctional Fuselage Demonstrator project earned the Clean Sky 2 consortium the prestigious JEC Innovation Award in 2025. This recognition highlights the breakthrough advancements in thermoplastic composites for commercial aircraft applications, paving the way for more sustainable and efficient manufacturing in the aerospace industry, as demonstrated by notable nominees Chase, Daher, and Avel. JEC Innovation Award 2025 winners explore new composite frontiers | CompositesWorld
- 2025, Victrex's groundbreaking LMPAEK polymer technology received prestigious recognition at the 2025 Ringier Technology Innovation Awards in China. The company earned top honors in the Raw Materials & Compounds category for its innovative LMPAEK granules and powders.
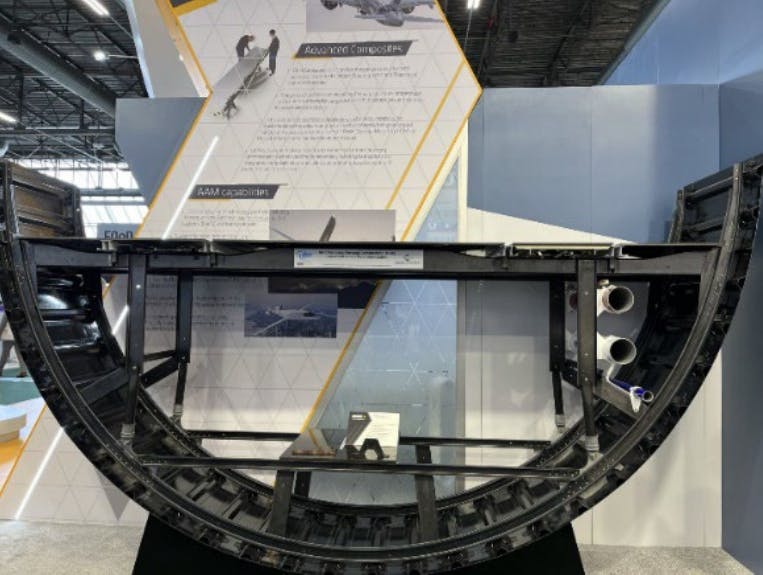
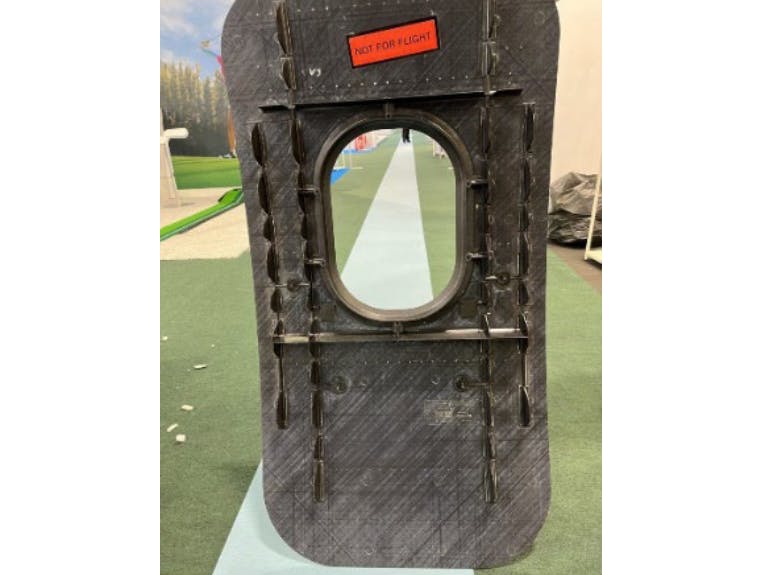
Supporting Aerospace Sustainability Goals
Furthermore, the use of LMPAEK™ polymers aligns with the industry's increasing focus on sustainability. These polymers are recyclable, which is a crucial factor in reducing waste and environmental impact. Additionally, the lightweight nature of LMPAEK™ polymers contributes to lower fuel consumption and reduced carbon emissions, making them a more eco-friendly option for aerospace manufacturers.
Enabling the Next Generation of Aerospace Advancements
The increased adoption of LMPAEK™ materials in the aerospace industry marks a significant milestone in the quest for more advanced and efficient aircraft components. With notable achievements and ongoing collaborations, the future looks promising for LMPAEK™ materials. As the industry continues to embrace LMPAEK™ polymer, it will undoubtedly contribute to the next generation of aerospace advancements, shaping the future of aviation.
About the Authors
Gilles Larroque joined Victrex in 2011, he is in charge of the Strategic Marketing activity for the Aerospace Business Unit. Prior to joining Victrex, from 2005 to 2011, Gilles worked in the medical devices industry, for Zimmer Spine, in product development for spinal applications. He started his career in 2001 as a R&D mechanical engineer consultant in various positions in aerospace and defence sectors. Gilles graduated with an engineer degree in mechanical system from the University of Technology or Troyes (France) in 2001. Starting in 1999, he graduated also with a Master of Science Thesis in engineering from Florida Atlantic University (USA) in 2001.
Ryan Herrmann joined Victrex in 2022 and is the Marketing Communications Manager for Aerospace and Additive Manufacturing. Ryan has 19 years’ experience in the manufacturing industry holding positions in Technical Service, Quality Assurance, and Inside Sales before transitioning into Marketing Communications. Ryan graduated from Gwynedd Mercy University in 2006 with a Bachelor of Science in Business Administration and a concentration in Marketing.
About the author
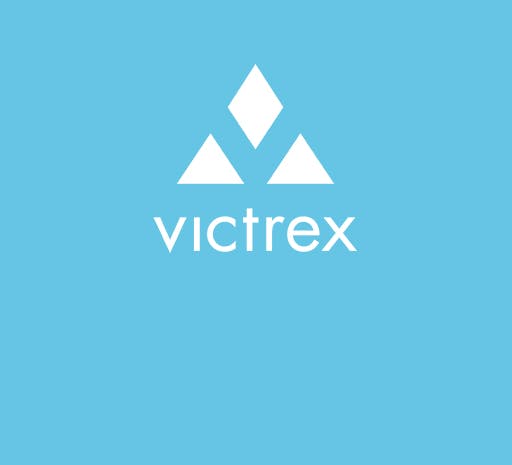