Polymer Crystallinity Explained: How it impacts material performance and manufacturing
In part 2 of the High-Performance Polymers series, we mentioned how the building blocks of the repeat unit of PEEK – the basic building block of the long PEEK polymer molecule – influenced its properties. In addition to the shape of the PEEK molecule, how it is arranged next to its neighbouring molecules is also important in determining the properties of the bulk polymer and this leads us into the field of polymer crystallinity.
Importance of Crystallinity for Polymers
The degree of crystallinity has a significant effect on the properties of a polymer. Semi-crystalline polymers like PEEK show an improvement in mechanical properties above the glass transition temperature, Tg, for example, with increased strength, stiffness and toughness compared to amorphous polymers. The crystalline domains essentially act as a kind of reinforcement of the rubbery amorphous phase above Tg, allowing semi-crystalline polymers to be used at higher temperatures.
Additionally, the crystalline regions scatter light to a greater degree, reducing optical transparency. Semi-crystalline polymers are therefore generally opaque, unless the size of the crystallites therein is smaller than the wavelength of visible light, as can happen for example in highly nucleated polypropylenes. Understanding and controlling crystallinity is therefore critical for tailoring the behaviour of polymers for different applications.
Crystals have an ordered and regular structure and have a well-defined melting point – think about ice, salt, sugar, amethyst. Amorphous (from those Greeks again, meaning “without form”) materials, like glass, have disordered structures which when heated up gradually soften above Tg before becoming viscous liquids
Crystals have an ordered and regular structure and have a well-defined melting point – think about ice, salt, sugar, amethyst. Amorphous (from those Greeks again, meaning “without form”) materials, like glass, have disordered structures which when heated up gradually soften before becoming viscous liquids.
Are crystalline polymers really fully crystalline?
Polymers can be amorphous or crystalline, depending upon a number of factors including the shape of their repeat unit, their molecular weight and their thermal history. Crystallinity in polymers is more complex than in other materials because of the long polymer chains. In some areas, the polymer chains align and pack together to form crystals; in other areas, the chains are disordered and cannot pack together, so semi-crystalline polymers tend to have crystalline regions dispersed within amorphous material. Strictly speaking, crystalline polymers are rarely, if ever, fully crystalline; they are semi-crystalline because there are always some amorphous regions caused by those long chains never fitting together perfectly.
Image adapted from pocketdentistry.com
The crystalline regions, being more closely packed, are denser than the amorphous regions, so if you know the density of the polymer crystal, you can calculate the degree of crystallinity of a polymer from its overall density. Typically, high-performance polymers of over about 25% crystallinity display the characteristics of a semi-crystalline polymer.
Generally, amorphous and semi-crystalline polymers have distinct characteristics:
Amorphous Polymers | Semi-crystalline Polymers |
Softens with increasing temperature | Well-defined melting point |
Good formability | Poor formability |
High transparency | Opaque |
Poor chemical resistance | Good chemical resistance |
Bonds well using adhesives | Difficult to bond with adhesives |
Poor fatigue resistance | Good fatigue resistance |
Poor wear resistance | Good wear resistance |
Used mainly in structural applications | Used in bearing, wear & structural applications |
PEEK is a semi-crystalline polymer and therefore it is used widely in bearing and wear applications and in applications requiring chemical and fatigue resistance. My colleague, Geoff Small, talks about why semi-crystalline polymers are more chemically-resistant in one of his blog posts.
In medical for example, PEEK-OPTIMA™ Ultra-Reinforced, a carbon fibre-reinforced PEEK (CFR-PEEK) has attracted interest. The material can offer the strength of metal in a composite polymer, suitable for trauma plates and nails, while remaining lightweight. With its favourable modulus of elasticity, it seems to provide the potential for enhanced stress absorption and load-bearing by allowing the design of a less stiff construct, which may support the healing process. It has also been shown to have a 50 times greater fatigue life than equivalent metal plates.*
Metal-free distal femur fracture fixation plate made with PEEK-OPTIMA Ultra-Reinforced polymer, a carbon fiber composite from Invibio; The trauma plate shown is not available for distribution or implantation - © Invibio
Where can semi-crystalline polymers be used?
Let's take a look at some of the opportunities that semi-crystalline PEEK and PAEK polymers and compounds can open up for different industries:
- In automotive, excellent strength and high heat resistance allow semi-crystalline PAEK materials to be used for structural components and parts under the hood. Due to their stiffness and wear resistance, they are also a great solution for gears, thrust washers and seal rings in transmission and drivetrain applications.
- In the oil and gas industry, PEEK and PAEK-based materials are used effectively in applications such as in sealing systems, electrical connectors, pump components, and other parts that must withstand extreme temperatures, high pressures, and chemically aggressive environments.
- The food industry is also one of the sectors that benefits from using PEEK and PEEK compounds. It can be used to replace metal parts with in food processing equipment, as it can improve hygiene and corrosion resistance.
- PAEK polymers and compounds in aerospace have been shown to be an effective solution for structural brackets, interior components, and other applications where weight savings and resistance to burning are critical.
As demonstrated, the unique properties of semi-crystalline PEEK offer a range of benefits in these, and many other challenging applications.
The influence of temperature control during injection moulding
Injection moulded PEEK is typically about 35% crystalline. Proper attention must be paid to the temperature of the injection mould tool to ensure it is hot enough to produce parts of consistent crystallinity (temperatures in the range 170 - 200°C are typically used in our laboratories): a common mistake is to use mould temperatures which are too low and this can result in parts with darker, amorphous skins.
Here’s the difference in extremis on some test specimens:
On real components which are more complex shapes than test specimens, this sort of appearance is typical if the mould temperature is too low:
So you can see PEEK’s crystallinity is influenced by how it is processed and especially by how it is cooled from the melt.
If you cool it really quickly – at more than 700°C/minute – the polymer chains do not get time to order themselves into crystalline domains, so you will make an amorphous PEEK. Victrex does this deliberately for some of its APTIV™ film products used in thermoforming applications. Consistent with the table above, the transparent, amorphous APTIV film softens and is easily formable at temperatures around 180°C, at which point it spontaneously re-crystallises (as the polymer chains are sufficiently free to move and re- organise themselves into crystalline domains at this temperature) and it becomes more opaque. Compare that to crystalline APTIV film, which can only be formed at temperatures above about 330°C.
Secondary crystallisation of PEEK during annealing – scientific debate ongoing It is also quite common in some applications – like extruded rods, shapes and plates – to post- anneal the parts, a process which can result in increased crystallinity. Again, annealing takes place at higher temperatures, typically around 230°C, and some re-crystallisation occurs, leading to products with up to 40% crystallinity. Additive manufactured PEEK parts, made by Selective Laser Sintering, can have around 45% crystallinity or more. Secondary crystallisation of PEEK during annealing has been debated for many years and even today the detailed mechanism is still the subject of scientific debate!
* Data on file at Invibio. Mechanical Benchmark of Carbon Fibre PEEK-OPTIMA™ Ultra-Reinforced vs Ti 6AI-4V Plates undergoing Static Testing per ASTM F382-99 (2008)
© Victrex plc. 2017. All rights reserved.
About the author
John Grasmeder, Chief scientist at Victrex
Dr John Grasmeder has over 25 years’ experience in the polymer industry, in R&D, commercial and business leadership positions at ICI, BASF, Hoechst and Shell joint ventures in both the UK and Germany. He has been with Victrex 11 years, and was Technical Director from 2010. He became Chief Scientist in 2016.
About the author
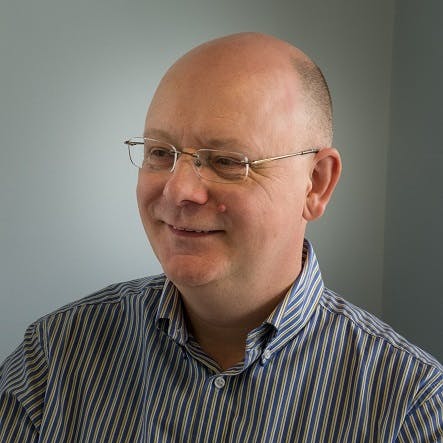