A Closer Peek at PEEK – HPP explained (part 2)
So what is PEEK?
PEEK or polyetheretherketone, belongs to a family of polymers called "aromatic polyketones" (more accurately "polyaryletherketones" or PAEKs). That means it's built up from the following building blocks:
R&D into PAEKs has its origins in the 1960’s but it wasn’t until 1978 that ICI (Imperial Chemical Industries) filed their patent on PEEK which was first commercialised as Victrex PEEK polymer in 1981.
"Aromatic", usually meaning distinctive or sweet-smelling, may seem a strange word here, but scientists use it to describe some molecules containing or made from ring-like structures (like the aryl building block above). Small molecules of this type, like toluene & naphthalene, have distinct odours, hence the name. PEEK itself however – like most thermoplastics – is odourless under normal conditions. From a chemical point of view, PEEK is a largely linear, semi-crystalline polymer. Here’s how the building blocks fit together and thus we get Ether Ether Ketone or EEK:
This “repeat unit”, shown in the square brackets above, is replicated many times – on average somewhere between 200-300 times – to make a single PEEK polymer chain. The P comes from the Greek “poly” meaning many, so many EEKs make PEEK. The aryl and ketone groups are fairly rigid and provide stiffness which means good mechanical performance combined with a high melting point. The ether groups provide some degree of flexibility, for toughness, and like the aryl and ketone groups are unreactive, so providing resistance to chemical attack. The regular structure of the repeat unit means that PEEK molecules can partially crystallise, and crystallinity provides a combination of wear, creep, fatigue and chemical resistance – more on this later.
The resulting polymer is widely regarded as one of the highest performing thermoplastics in the world. Compared to metals, PEEK-based materials are very light weight, easily shaped, resistant to corrosion and can have considerably higher specific strength (strength per unit weight).
Designing to the needs of the application
When we make PEEK, we use a process which controls the length of the chains, or molecular weight. PEEK with longer chains (high molecular weight or MW) tends to be tougher and more impact-resistant than PEEK with short chains. However, high MW polymers are very viscous when molten which can limit their ability to fill small moulds. Low MW PEEK is less impact-resistant but flows much better in the melt so can make small intricate parts easily.
A set of attractive properties
PEEK does not offer merely two or three properties that mark it as the polymer of choice when high performance is required; it has a whole variety of them. They include:
-
High heat resistance
Tests have shown that VICTREX PEEK polymer has a continuous use temperature of 260°C (500°F). This can make it suitable for use in a wide range of thermally aggressive environments, such as those found in the process industries, in the oil and gas sector and inside the engines and transmissions of millions of vehicles. PEEK is able to tolerate friction and resist wear in dynamic applications like thrust washers and seal rings.
-
Chemically unreactive
PEEK is able to resist the damage that can be inflicted in chemically aggressive operational environments, such as downhole in wells the oil & gas industry, in gears in machinery & automotive applications. It can resist jet fuel, hydraulic fluids, de-icers and insecticides used in the aerospace industry. This holds true over wide ranges of pressure, temperature and time.
-
Mechanically strong
PEEK demonstrates excellent strength and stiffness over a wide temperature range. PEEK-based carbon fibre composites have specific strength many times that of metals and alloys. "Creep" refers to a material becoming permanently deformed over an extended period of time when under constant applied stress. “Fatigue” refers to the brittle failure of a material under a repeated cyclic loading. PEEK has both high creep and fatigue resistance thanks to its semi-crystalline structure and has been shown to be more durable than many other polymers and some metals over a long and useful lifetime.
-
Difficult to ignite or burn
PEEK has excellent flammability performance. It resists combustion up to almost 600°C. When it can be made to burn at very high temperatures, it will not support combustion and it emits little smoke. This is one reason why PEEK is widely used in commercial aircraft.
-
Re-processable and recyclable
The PEEK molecule is very stable, so the polymer can be re-melted and reprocessed again and again with minimal change to its properties. This helps its environmental footprint and can ensure that waste material from manufacturing processes can be re-used economically.
-
There's more!
As a thermoplastic PEEK can be processed using conventional thermoplastic processing equipment for injection and compression moulding as well as extrusion. It is very versatile and increasingly used for improved part performance, durability, weight saving and overall reduced lifetime system cost. No wonder it’s replacing metals and alloys!
Across many industries and critical environments, material experts, part designers and purchasers have to decide whether PEEK is the material of choice to enable advances in performance, weight reduction, energy consumption, assembly time, cost savings or stick to traditional metals and alloys.
About the author
John Grasmeder, Chief scientist at Victrex
Dr John Grasmeder has over 25 years’ experience in the polymer industry, in R&D, commercial and business leadership positions at ICI, BASF, Hoechst and Shell joint ventures in both the UK and Germany. He has been with Victrex 11 years, and was Technical Director from 2010. He became Chief Scientist in 2016.
About the author
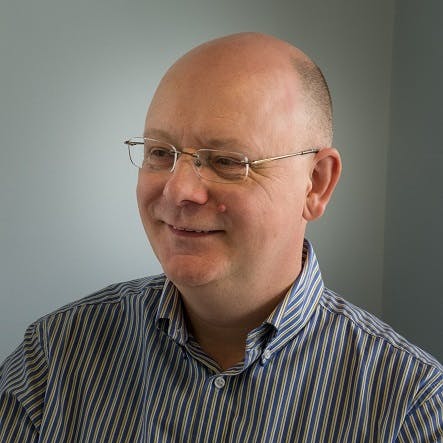