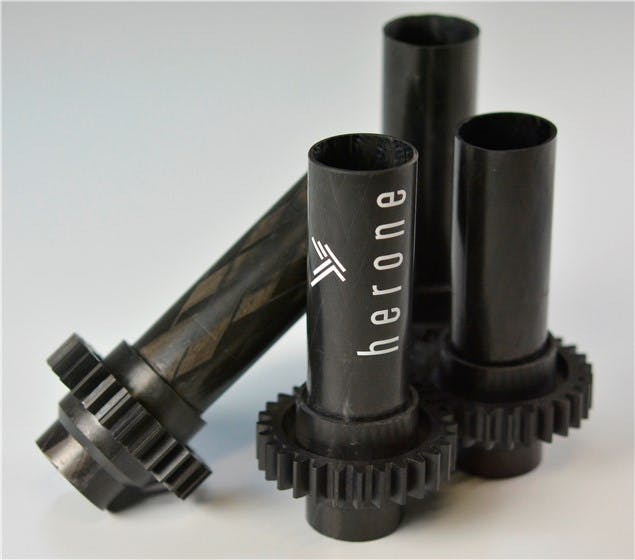
Die herone GmbH aus Dresden hat den prestigeträchtigen JEC Innovation Award 2019 in der Kategorie Aerospace Application für ein ganz aus thermoplastischen Kunststoffen bestehendes Antriebswellensystem mit angespritztem Zahnrad erhalten. Die Technologie birgt enormes Potenzial für Leichtbau-Anwendungen in der Luftfahrt, die Victrex mit seiner neuen Generation von PAEK-Hochleistungspolymeren ermöglicht.
Die Antriebswelle besteht aus einem aus thermoplastischen UD-Tapes geflochtenen Vorformling, einem sogenannten „organoTube“, der zuerst zu einem stoffschlüssigen Composite-Rohr konsolidiert und anschließend im Spritzgusswerkzeug mit VICTREX™ PEEK 90HMF40 überspritzt wird. Die unidirektionalen Tapes bestehen aus kontinuierlichen Kohlenstofffasern, die mit VICTREX AE™ 250 imprägniert wurden. Das Verfahren wurde vom Institut für Leichtbau und Kunststofftechnik (ILK) der TU Dresden und von der herone GmbH entwickelt, um hochwertige Hohlprofile aus endlosfaserverstärkten PAEK-Verbundwerkstoffen herzustellen. Die Kombination mit dem Spritzguss erlaubt dabei, weitere Funktionen zu integrieren; in diesem Fall ein Zahnrad mit stoffschlüssiger Anbindung und geometrischen Hinterschnitten, die höhere Torsionsfestigkeit ermöglichen.
„Wir freuen uns sehr über diesen JEC Award. Er bedeutet jedem, der im spannenden Feld der Verbundstoffe arbeitet, sehr viel“, sagt Daniel Barfuss, Managing Partner bei der herone GmbH. „Wir führen in unserer Lösung Innovationen zusammen, das heißt die Hohlprofiltechnologie und die von Victrex entwickelte Technik des Hybrid Mouldings. Das ist Teamarbeit in Aktion. Gemeinsam definieren wir die Grenzen der Verbundstofftechnologie in der Luftfahrt neu.“
Enormes Potenzial für kürzere Zykluszeiten und Fertigung im industriellen Maßstab
Durch die Nutzung thermoplastischer Tapes zum Formen der organoTubes ist der komplexe und zeitaufwendige Prozessschritt des Imprägnierens der Karbonfasern mit thermoplastischem Matrixmaterial bereits vor der Formgebung abgeschlossen. Dies eröffnet Potenzial für deutlich kürzere Zykluszeiten und Effizienzsteigerungen bei den Herstellungsprozessen für Verbundstoffprofile. Darüber hinaus ermöglicht das Flechten hohe Legeraten und macht den Prozess auch für die industrielle Fertigung in großem Maßstab geeignet.
Das Hybrid-Spritzgussverfahren basiert auf der sehr guten Verschweißbarkeit der beiden Materialien. Es werden kohäsive Bindungen auf Molekülebene zwischen der Welle und dem Zahnrad erzeugt. Gleichzeitig wird die Antriebswelle beim Überspritzen thermogeformt, sodass zwischen dem Zahnrad und der Antriebswelle eine stoffschlüssige Verbindung mit Hinterschnitten entsteht, die die Festigkeit des CFK-Bauteils weiter erhöhen.
Die Schmelztemperatur von VICTREX AE 250 liegt ungefähr 40 °C unter der des mit kurzen Carbonfasern verstärkten VICTREX PEEK 90HMF40. Dieser Unterschied bedeutet, dass das Matrixpolymer, aus dem die Welle hergestellt ist, vor dem Umspritzen nicht über seine Schmelztemperatur hinaus vorgewärmt werden muss. Dieser Verarbeitungsansatz von Victrex ist als „Hybrid Moulding“ bekannt und führt zu erheblich verbesserter Ressourceneffizienz, Prozesssicherheit und Verbindungsfestigkeit.
herone und Victrex erwarten, dass die neue thermoplastische Lösung wesentliche Vorteile mit sich bringt, zum Beispiel:
• Verbesserte Teilequalität, zum Teil aufgrund der Flexibilität des Flechtprozesses der UD-Tapes
• Kurze Zykluszeiten, da die Konsolidierungstechnologie von herone Zykluszeiten im Bereich von Minuten ermöglicht
• Kostensenkung durch intelligentes Design mit integrierter Funktionalität, wodurch die Anzahl der Bauteile und die Montagekosten gesenkt werden
• Leistungsverbesserung, da kohäsive stoffschlüssige Bindungen und Hinterschnitte die Festigkeit erhöhen
• Finale Formgebung der thermoplastischen CFK-Rohre während des Umspritzens bildet die formschlüssige Geometrie mit den speziellen Eigenschaften (z. B. eine sternförmige Innenkontur)
„In der Luftfahrtindustrie sind die Kosten und der Fertigungsdurchsatz die zentralen Antriebsfaktoren für Innovationen“, erklärt Frank Schemm, Leiter des Vertriebsteams Aerospace bei Victrex. „herone und Victrex entwickeln gemeinsam neuartige Verbundstofflösungen für die kommerzielle Luftfahrt, die eine schnellere Bauteilefertigung in höheren Stückzahlen bei potenziellen Kosteneinsparungen ermöglichen. Innovative Konsolidierungstechniken für thermoplastische Materialien unterscheiden sich erheblich von der Verarbeitung von Metall oder Duroplasten. Voll funktionsfähige Designmerkmale können in weniger Fertigungsschritten integriert werden. Wir gratulieren herone zu dieser Auszeichnung. Für diese Verbundstofflösung wird aufgrund der sich schnell entwickelnden Branche mit Sicherheit eine hohe Nachfrage bestehen. Insbesondere der stark wachsende Bereich elektrisch angetriebener Fluggeräte, der sogenannten Lufttaxis, erfordert viel höhere Fertigungsraten als die herkömmlichen klassischen Flugzeugprogramme.“
Das ganz aus thermoplastischem Kunststoff bestehende, mit integriertem Zahnrad umspritzte Antriebswellensystem von herone ist vom 2. bis 4. April auch auf der AIX in Hamburg am Victrex-Stand 6A95 zu sehen.
+++
Über herone
Dank seines Know-hows in den Bereichen Design, Material und Verarbeitung kann herone die fortschrittlichen Materialeigenschaften thermoplastischer Verbundstoffe nutzen, um einen neuen Standard für die Leistungsfähigkeit seiner Produkte zu setzen. Mit seiner Technologie nutzt herone die Eigenschaften der thermoplastischen Verarbeitung, um eine effiziente, skalierbare Serienfertigung von Profilen aus thermoplastischen Verbundstoffen zu ermöglichen und durch Kombination fortschrittlicher Lösungen für die Nachbearbeitung die Funktionalität zu verbessern. Die Kombination der Vorteile thermoplastischer Kunststoffe mit dem Know-how und der Technologie von herone ermöglicht es dem Unternehmen, die Leistung von Bauteilen entsprechend der Vorgaben genau anzupassen und sie mit äußerster Effizienz zu fertigen. Weitere Informationen finden Sie auf der Website https://herone.de/