LMPAEK™ kurz erklärt - und warum es sich so gut für Verbundwerkstoffe und additive Fertigung eignet.
In meinem letzten Blog "PEEK oder PAEK, was steckt hinter dem Begriff?" haben wir uns mit der PAEK-Familie und einigen ihrer Mitglieder befasst und mit den jüngsten LMPAEK™-Neuzugängen, dem VICTREX AE™ 250 UD-Band und dem VICTREX AM™ 200 Filament, abgeschlossen, die auf Co-Polymeren mit zwei statt einer Wiederholungseinheit basieren.
Betrachten wir also die Co-Polymere im Allgemeinen, die auch in vielen anderen Polymerfamilien vorkommen. Ein lineares Polymer, das aus einer einzigen sich wiederholenden Einheit, A, besteht, bildet Polymerketten, eine Rückgratstruktur, die wie folgt aufgebaut ist:
-A-A-A-A-A-A-A-A-A-A-A-A-A-A-A-
Bei Copolymeren, die aus zwei sich wiederholenden Einheiten, A und B, bestehen, gibt es jedoch verschiedene Möglichkeiten. Wenn A und B in gleicher Anzahl vorhanden sind, könnte sich eine regelmäßige, alternierende Struktur ergeben:
-A-B-A-B-A-B-A-B-A-B-A-B-A-B-A-B-
Solche Strukturen sind tatsächlich selten. Weitaus häufiger kommt es zu einer statistischen oder zufälligen Kombination der sich wiederholenden Einheiten, denn das liegt in der Natur der Polymerchemie! Bei 75 % A- und 25 % B-Wiederholungseinheiten könnte man sich ein solches Grundgerüst vorstellen:
-A-A-B-A-B-A-B-B-A-A-A-B-A-A-A-A-A-B-A-A-
Es gibt aber auch eine andere Möglichkeit, ein so genanntes Block-Copolymer, bei dem die sich wiederholenden Einheiten, Sie ahnen es, in Blöcken auftreten. Nimmt man wieder das Verhältnis von A und B von 70:30, könnte das so aussehen:
-A-A-A-A-B-B-B-B-B-B-A-A-A-A-A-A-A-A-A-A-
Die Art und Weise, wie die sich wiederholenden Einheiten in der Hauptkette angeordnet sind, kann die Geschwindigkeit, mit der das Polymer kristallisiert, und auch das Ausmaß der Kristallinität beeinflussen. Das Polymer kann in diskreten A- und B-Bereichen kristallisieren oder in ungeordneter Form oder irgendwo dazwischen. Dies hat einen entscheidenden Einfluss auf die makroskopischen Eigenschaften des Polymers - die mechanischen Eigenschaften wie Steifigkeit und Zähigkeit, seine Bruchfestigkeit und sogar seine chemische Beständigkeit.
Die Hauptmotivation für die Entwicklung dieser PAEK-Copolymere bestand darin, sie bei wesentlich niedrigeren Temperaturen verarbeiten zu können, indem der Schmelzpunkt Tm gesenkt und gleichzeitig die Glasübergangstemperatur Tg beibehalten wurde, so dass die Hochtemperatureigenschaften erhalten bleiben. Aber auch die Verarbeitbarkeit dieser Polymere für die unterschiedlichen Prozesse, in denen sie eingesetzt werden, konnte verbessert werden. Betrachten wir sie der Reihe nach:
VICTREX AE™ 250 UDT - Entwickelt für Verbundwerkstoffe
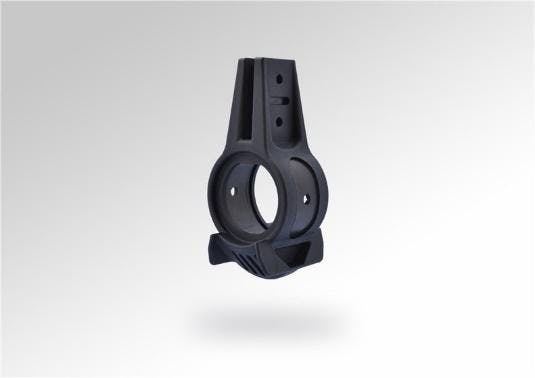
Anfangs hatten wir uns zum Ziel gesetzt, das neue Polymer besser für die Verarbeitung von Verbundwerkstoffen geeignet zu machen als PEEK. Ein Teil dieser Aufgabe war die niedrigere Verarbeitungstemperatur, aber wir zielten auch auf die Geschwindigkeit der Kristallisation ab. PEEK kristallisiert extrem schnell, was bei Spritzgussanwendungen von Vorteil sein kann, während wir zur Verarbeitung von Verbundwerkstoffen ein Material wollten, das langsamer kristallisiert, da dies den Schichtaufbau und die Konsolidierung erleichtert, insbesondere außerhalb des Autoklaven.
Hochwertige Verbundwerkstoff-Laminate
Es gibt zunehmend Belege dafür, dass dieser Ansatz gut funktioniert. So haben wir gemeinsam mit Daher gezeigt, dass mit VICTREX AE™ 250 UDT wesentlich dickere, hochwertige Verbundwerkstofflaminate hergestellt werden können, aktuell bis zu 176 Lagen im Vergleich zu 32 Lagen als Norm.

Thermoplastische Verbundwerkstoffe entsprechen der Duroplast-Layup-Geschwindigkeit
In Zusammenarbeit mit Electroimpact wurde kürzlich das Ziel erreicht, die Legegeschwindigkeit von Duroplasten zu erreichen. Aufgrund der niedrigeren Tm eignet sich VICTREX AE™ 250 UDT auch ideal für das Umspritzen mit Compounds wie beispielsweise VICTREX PEEK 150CA30: Das PEEK und das Copolymer sind in der Schmelze vollständig mischbar, sodass die Oberfläche der Verbundstoffplatte mit dem umspritzten Compound verschmilzt und eine gute Schnittstellenhaftung entsteht.
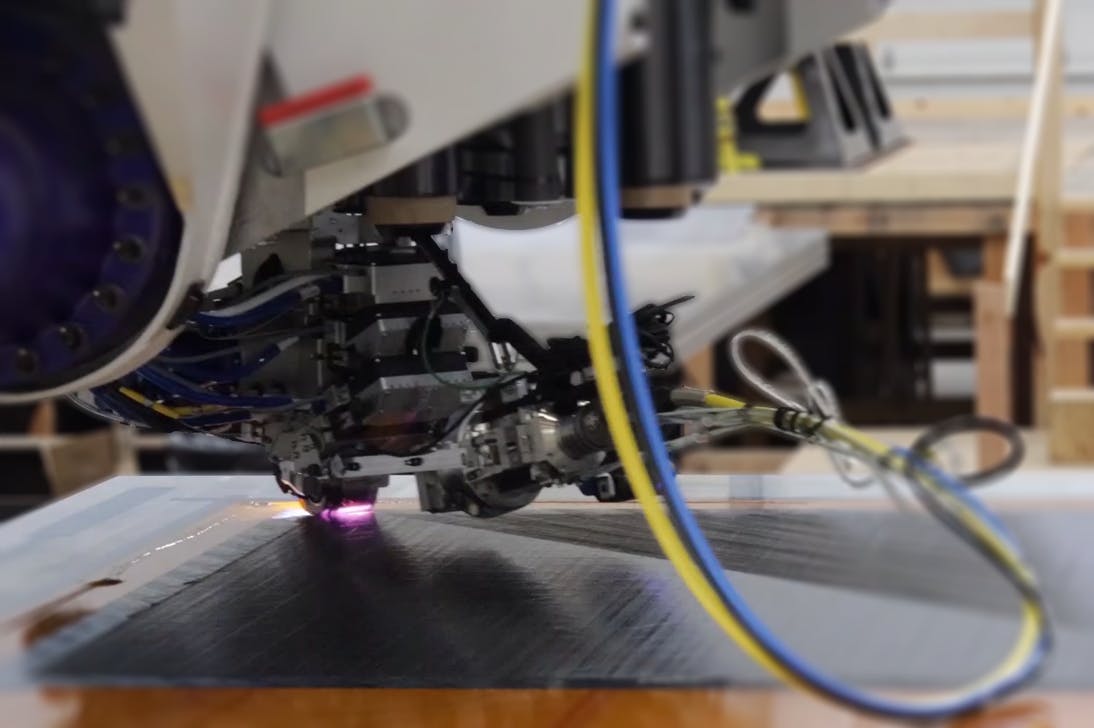
VICTREX AM™ 200 filament für Additive Fertigung / 3D Druck
Traditionelle Herausforderungen beim Druck von PAEK-PolymerenBevor wir das VICTREX AM™ 200 Filament entwickelt haben, galt es als allgemein anerkannt, dass der 3D-Druck von Teilen aus teilkristallinen PAEKs eine Herausforderung darstellt: Sie haften nur schlecht zwischen den einzelnen Schichten. Das liegt daran, dass nach dem Druck einer Schicht in der Regel eine Zeitspanne vergeht, bis die nächste Schicht aufgedruckt wird und die untere Schicht bereits kristallisiert und abgekühlt ist.
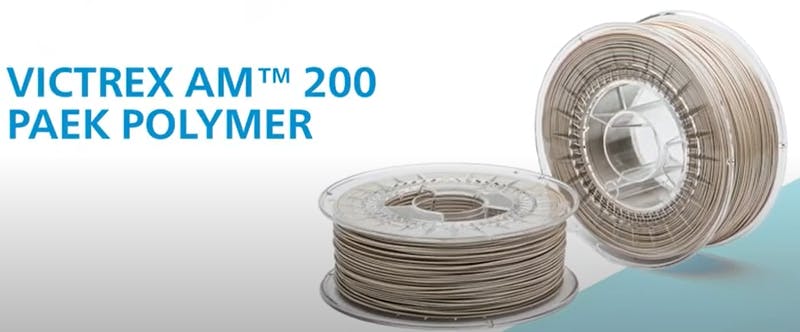
Dies führte zu schlechteren Eigenschaften in der vertikalen Z-Richtung als in der X-Y-Ebene, wobei die Z-Richtung manchmal nur 13-25 % so stark war wie die X-Y-Richtung. Neue Technologien, wie Bond 3D, greifen dieses Problem jedoch auf.
VICTREX AM 200 ermöglicht eine niedrigere Verarbeitungstemperatur und eine deutlich langsamere Kristallisationsgeschwindigkeit, so dass die Festigkeit von Teilen in Z-Richtung bis zu 80 % so hoch sein kann wie in der X-Y-Ebene und die Duktilität mehr als dreimal so hoch ist wie bei einigen PEEK-Typen.
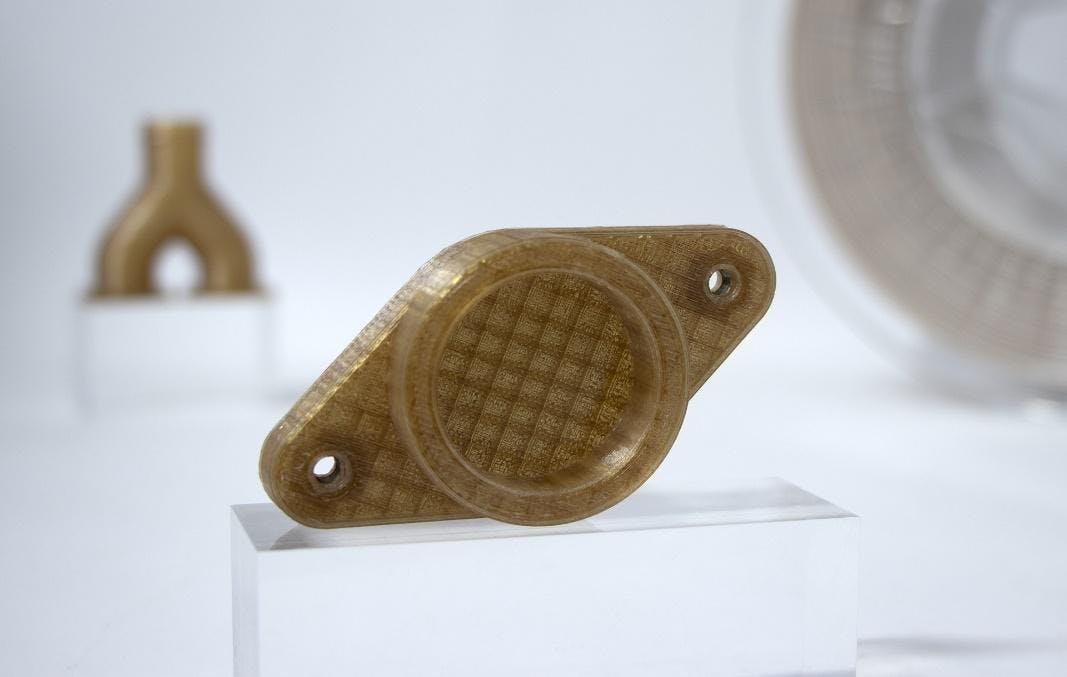
VICTREX AM™ 200 - Entwickelt und optimiert für die Additive Fertigung.
Unsere Partner am Centre for Additive Layer Manufacturing (CALM) der Universität Exeter haben zusammen mit meinen Kollegen die Gründe dafür eingehend untersucht und uns ein umfassendes Verständnis dafür vermittelt, warum dies so gut funktioniert.
Zusammenfassung
Ich hoffe, dass ich einige der Vorteile von PAEK-Copolymeren verdeutlichen konnte. Auch wenn PEEK noch viele Jahre lang im Einsatz sein wird, werden diese neuen Co-Polymere dazu beitragen, verschiedene technische Herausforderungen zu lösen, und fortschrittliche Materiallösungen auf der Basis von PAEK werden zukünftig mehr denn je in spannenden neuen Anwendungen zum Einsatz kommen.
© Victrex plc. 2021. Alle Rechte vorbehalten.
Disclaimer
Über den Autor
John Grasmeder, Leitender Wissenschaftler bei Victrex
Dr. John Grasmeder verfügt über mehr als 25 Jahre Erfahrung in der Polymerindustrie, wo er bei ICI, BASF, Hoechst und Shell Joint Ventures in Großbritannien und Deutschland in Forschung und Entwicklung sowie in leitenden Positionen in der Unternehmensführung tätig war. Er ist seit 2005 bei Victrex tätig und war seit 2010 technischer Direktor. Im Jahr 2016 wurde er Leitender Wissenschaftler.
Über den Autor/die Autorin

Entdecken Sie den Victrex Blog
Alle Blogartikel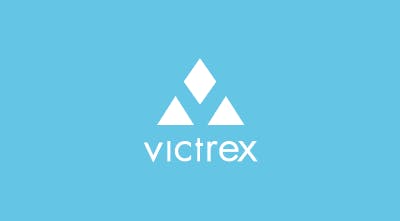
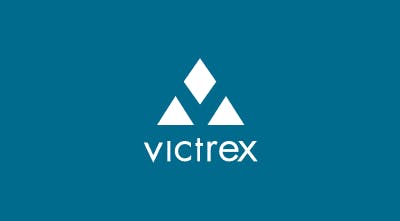

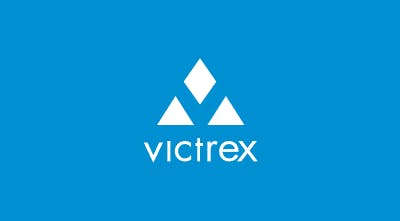